污泥熱解氣化技術
污泥熱解氣化技術是華天環保污泥全流程處理技術的核心技術之一。
一、 什么是熱解氣化?
熱解氣化焚燒是一種傳統的工業化生產技術,廣泛應用于煤炭、石化等行業。
概念:熱 解 pyrolysis: 有機物在無氧或貧氧的環境下加熱,使之轉化為氣態、液態、固態的可燃物質的化學反應過程。
反應原理 :有機固體廢棄物+熱量,在無氧/貧氧狀態下,生成可燃氣+爐渣。
二、 污泥氣化過程
污泥氣化技術是利用有機質在高溫貧氧條件下裂解的性質,將污泥烘干后投入密閉蓄熱氣化爐內,經過900-1100℃的高溫貧氧氣化環境,使污泥中的有機成分裂解揮發,轉化為以一氧化碳、氫氣、烷類氣體為主的可燃氣體,污泥中的無機物以殘渣形式排出。如圖1
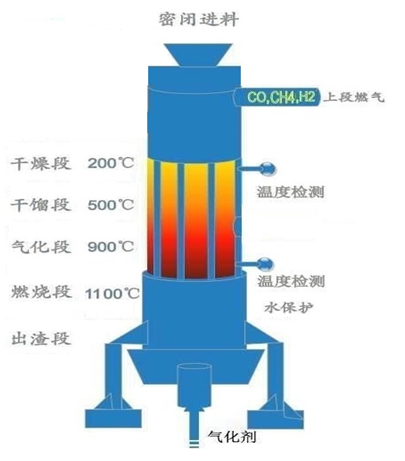
圖1
1.干燥:污泥進入氣化爐,在下降的過程中與高溫熱解燃氣接觸,污泥中的水變成蒸汽和熱解燃氣一起排出爐外,污泥逐步變干燥。
2.干餾:干燥后的污泥,在200-500℃的貧氧條件下干餾,生成烷類(CmHn)、一氧化碳(CO)、焦油等可燃氣體和水蒸氣(H2O),從爐體上端排氣口排出。
3.氣化:經過碳化后的污泥,主要殘留物是焦炭和無機不可燃物,在600-1000℃高溫下,與燃燒產生的CO2反應生成CO,部分碳化物通過水蒸氣的作用,發生氧化還原反應生成CO、H2等可燃氣體,從爐體下段排氣口排出。
4.燃燒:污泥氣化反應完成后,剩余固定炭在800-1100℃高溫下,與氧氣反應生成CO2,為整個氣化反應過程提供熱量。
三、 污泥氣化工藝流程
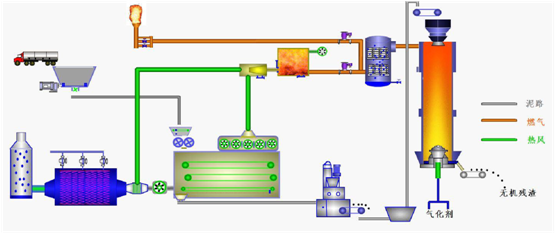
圖2
四、 技術優勢
1.遏制二噁英:從原理上遏制了二噁英類物質的生成。尾氣排放中二噁英濃度遠低于國家標準的0.1ng/m3 。污泥氣化后可燃氣燃燒尾氣二噁英濃度為0.045ng/m3。
2. 無飛灰產生: 成型氣化、流速低、料層高
3. 固化重金屬 :高溫燃燒,包裹固化重金屬
4. 減量化明顯 :以含水率80%計,減量化高達90%以上
5. 無害化徹底: 處理溫度高達1100℃
6. 資源化利用:污泥自身有機質能源被有效利用
對比發現:尾氣排放中二噁英濃度遠低于國家標準的0.1ng/m3
污泥焚燒尾氣二噁英濃度約0.3ng/m3,而污泥氣化后可燃氣燃燒尾氣二噁英濃度為0.045ng/m3,遠遠低于國家標準。
五、遏制二噁英的原理
二噁英的分子結構是由1或2個氧原子聯結2個被氯原子取代的苯環,氧、氯以及苯環是二噁英生成的基本條件。污泥熱解氣化過程中,燃燒段以上完全處于貧氧狀態,沒有氧原子參與反應,故不會產生二噁英;污泥到達燃燒段時,有機物全部干餾,僅剩炭在燃燒,沒有含氯苯環產生,所以從避免了二噁英類物質生成的條件。
二噁英的分子結構(圖3)
二噁英檢測報告
六、無飛灰產生的原理
飛灰屬于危險廢物,隨尾氣排放,造成煙塵污染,使煙氣處理難度增加;同時也是二噁英類有毒物質及重金屬附著和傳播的載體。
氣化焚燒無飛灰產生的原因:
1.污泥在進入氣化設備前已被成型;
2.污泥在設備內部處于相對靜止狀態;
3.氣化爐內氣流速度極低,灰不易帶出;
4.設備內有4-5米的料層厚度,渣層在設備最底部,料層起到很好的過濾作用,灰渣不易帶出。
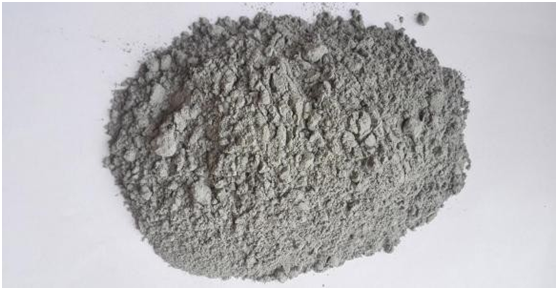
七、固化重金屬的原理
在高溫狀態下,污泥中所含的重金屬成分變成氧化物牢牢地包裹固化,避免了重金屬在自然環境中浸出,殘渣中的重金屬離子被包裹或被氧化,不再產生毒性。將殘渣用于建筑材料,制作水泥、免燒磚,或作為路基材料利用。
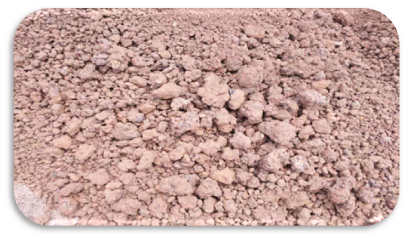
高溫熔融殘渣
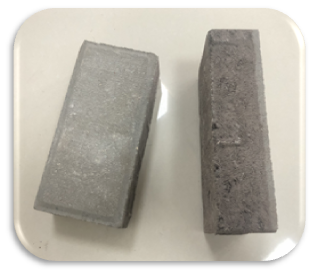
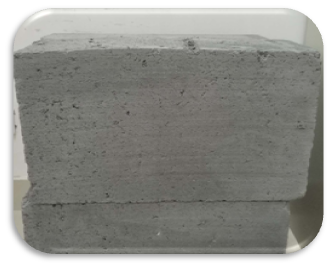
殘渣制作的免燒磚 殘渣制作的加汽塊
氣化殘渣重金屬檢測遠低于國家標準 (見檢驗報告)
經高溫氣化處理后的爐渣浸出液做重金屬檢測,含量低于國家《城鎮污水處理廠污泥處置單獨焚燒用泥質》標準(CJ/T290-2008),可用作路基材料或者制作免燒磚。
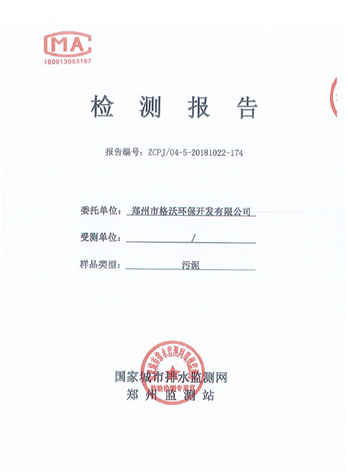
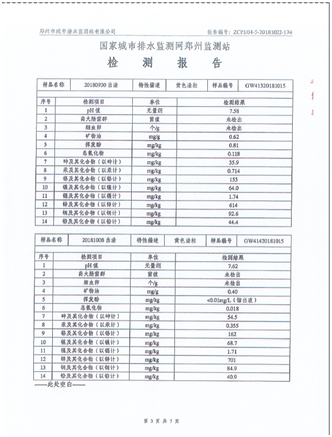
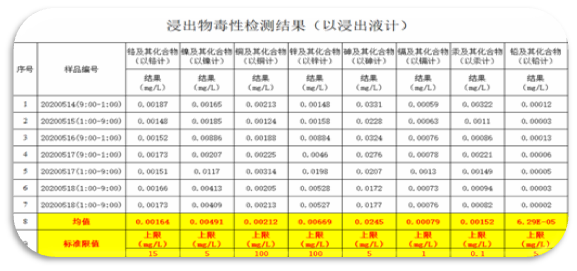